
How to use the din rail channel machine?
2025-06-13 12:00Introduction to Din Rail Channel Machine
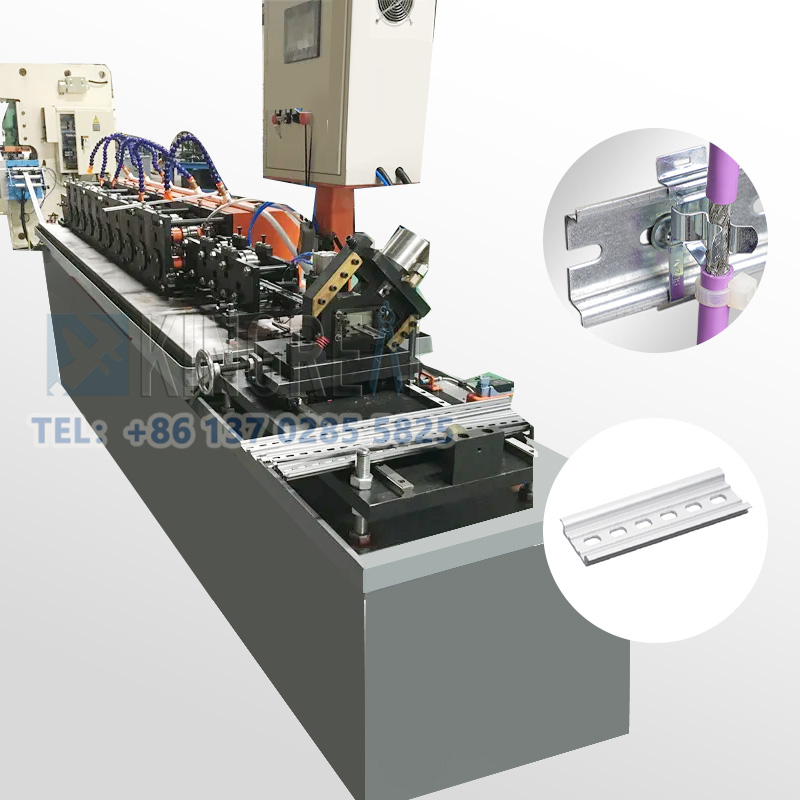
Din Rail Channel Machine is a highly efficient equipment specially used for producing din rails, usually used to produce 35mm x 7.5mm and 35mm x 15mm din rails. The din rail making machine can produce a variety of common types of din rails, including Top Hat Section Din Rail, C Section Din Rail and G Section Din Rail. These din rails are widely used in the installation of electrical equipment, such as circuit breakers, relays and choppers, to ensure the safe operation of electrical systems.
Din Rail Channel Machine has been widely used in many countries around the world, especially in regions with developed electrical equipment manufacturing industries, such as Germany, the United States, France, Italy, India, Indonesia and China. The demand for electrical din rails in these countries continues to grow, driving the market development of din rail making machine. With the acceleration of global energy transformation and electrification, the use of din rail channel machine is also expanding, covering more industry applications.
Workflow of Din Rail Channel Machine
Uncoiler straightener 2 in 1 ↓ Servo feeder ↓ Guide device ↓ Hydraulic Punch ↓ Roll forming machine ↓ Shear device (including knife) ↓ Finished product rack | ![]() |
Good Way to Use Din Rail Channel Machine
The process of using the din rail making machine can be divided into several key steps, combined with the din rail channel machine’s workflow to ensure the smooth progress of production.
1. Preparation | Before starting to use the din rail making machine, the following preparations need to be made: Material preparation: Make sure that the coil used meets the specification requirements, such as thickness and material. It is generally recommended to use high-strength, corrosion-resistant materials to increase the service life of the din rail. Equipment inspection: Check the various components of the din rail channel machine to ensure that they are not damaged and operate normally. Pay special attention to the hydraulic system and electronic control system to ensure the stability of the din rail making machine during production. Parameter setting: According to the specifications of the required din rail, adjust the parameters on the control panel, including material width, cutting length and forming speed. This step is crucial to ensure the quality of the finished product. |
2. Start the din rail channel machine | When starting the din rail making machine, follow the steps below: Unwinding and leveling: First, use the decoiler and leveling machine to place the coil on the machine to ensure that the material is neat and wrinkle-free. Ensuring the flatness of the material can reduce problems in the subsequent forming process. Servo feeding: The material is fed into the din rail channel machine through the servo feeder to ensure the accuracy of the feeding to avoid production errors. The precise control of the servo system can significantly improve production efficiency. |
3. Processing process | During the processing, the din rail making machine will automatically produce according to the set process: Guide device: The guide device ensures that the material remains stable before entering the hydraulic punching machine to prevent deviation. Correct guidance can reduce material waste. Hydraulic punching: The hydraulic punching machine will punch holes in the material to achieve the necessary connection function in the subsequent forming process. The accuracy of the punching directly affects the use effect of the din rail. |
4. Forming and Cutting | After punching, the material will enter the forming stage: Roller forming: The roller forming device of the din rail channel machine gradually forms the material to form the required din rail structure. During this process, the rollers of the machine gradually shape the material to ensure that every detail meets the design requirements. The thickness and shape of the finished product should be checked regularly during the forming process to ensure that it meets the standards. Cutting: Once the forming is completed, the cutting device will cut the finished product according to the set length. Ensuring the accuracy and neatness of the cutting is a key step. The state of the cutting tool has a great influence on the cutting quality, so the tool should be maintained and replaced regularly. |
5. Finished product output | Finally, the finished product will be neatly output through the finished product output rack to facilitate subsequent packaging and transportation: Quality inspection: Before the finished product is output, a quality inspection is carried out to ensure that the size, shape and hole position of the din rail meet the standards. Quality control is an important part of ensuring product reliability. Storage and transportation: Qualified finished products can be stored or directly transported to the customer's designated location. Reasonable storage methods can protect the product and prevent damage during transportation. |
Maintenance and Care for Din Rail Making Machine
In order to ensure the long-term stable operation of the din rail channel machine, regular maintenance and care are necessary:
Regular inspection: Regularly check the various parts of the din rail making machine, especially the hydraulic system and the electronic control system, to ensure that there is no oil leakage or failure.
Lubrication maintenance: Lubricate the moving parts of the machine on time to reduce wear and improve work efficiency.
Cleaning maintenance: Keep the din rail making machine clean and regularly clean up the metal chips and dust generated during the production process to avoid affecting the normal operation of the din rail making machine.
The din rail channel machine is an indispensable and important equipment in the manufacture of electrical equipment. Its efficient and automated production capacity provides great convenience for enterprises. Through reasonable use of processes, operators can quickly and accurately produce din rails that meet the requirements to meet market demand.
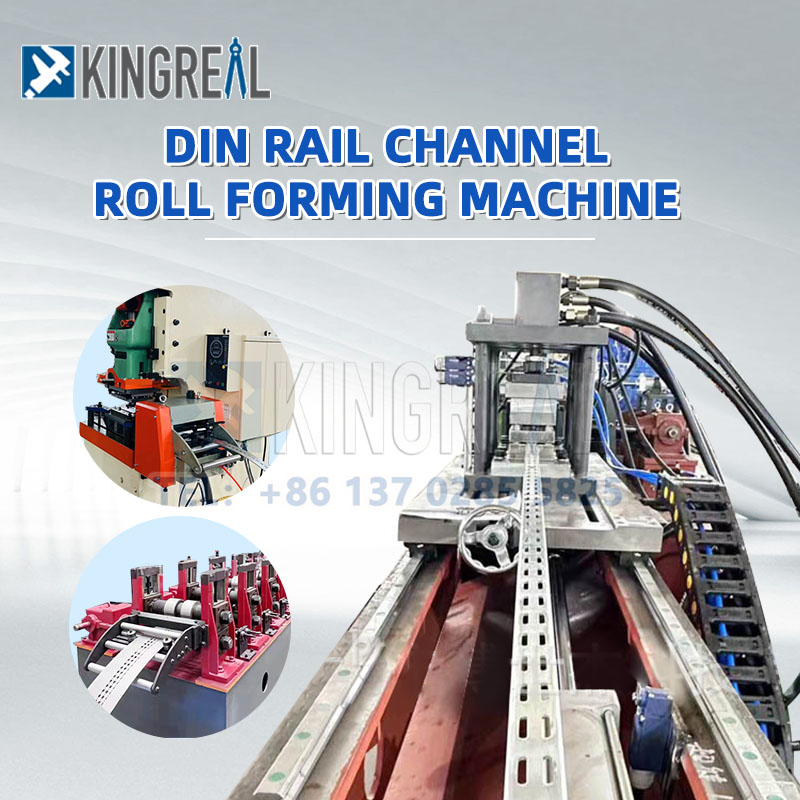
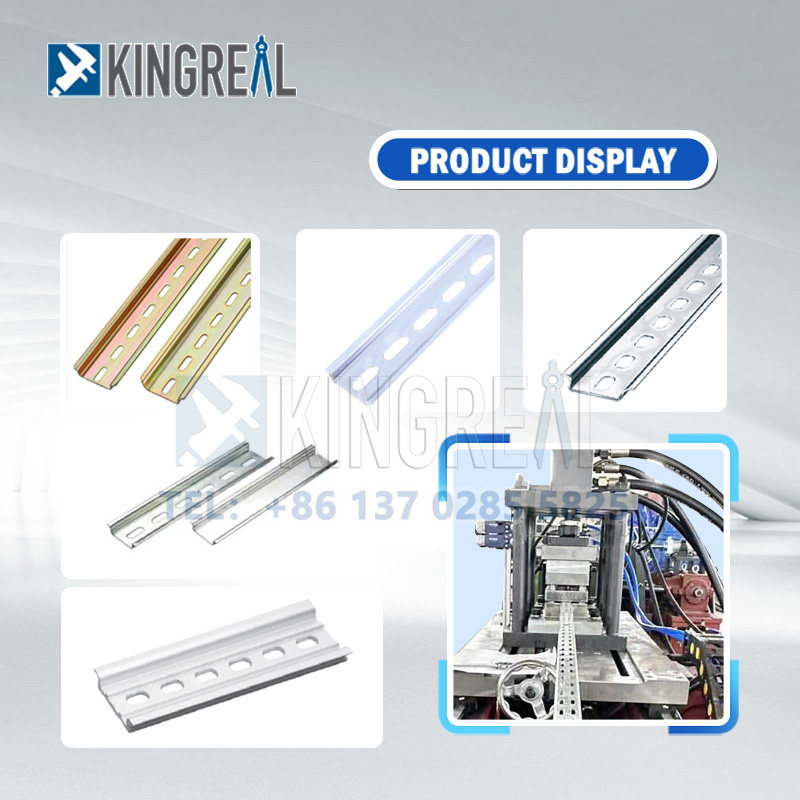
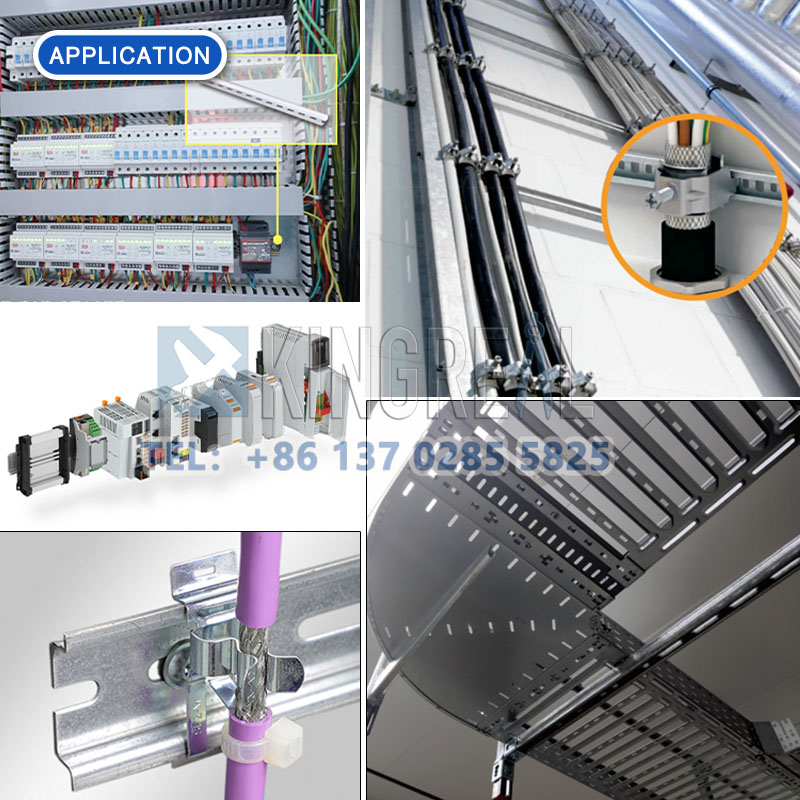
With the continuous development of the electrical industry, the application of din rail making machines will become more and more extensive, and it will become an important force to promote the development of the electrical equipment industry. Choosing a suitable din rail making machine can not only improve production efficiency, but also ensure product quality, bringing higher competitive advantages to enterprises. Through continuous technological innovation and market expansion, the future of din rail making machines will be brighter.